Using Polycarbonates In Biomedical Applications
Polycarbonates are a group of thermoplastics polymers with Bisphenol (A) parts and carbonate groups in their chemical structure. Polycarbonates are strong, rigid, transparent, and have reasonably high heat resistance, making them optimal materials for industrial and medical trades alike.
In industrial applications, manufacturers use different blends of polycarbonates to enhance the desired properties of the product they are constructing. For example, they can be used to increase the ductility and strength of a given material at varying temperatures. Polycarbonates are also crucial in medical applications such as surgical instruments, connectors, and needle-free injections.
Watch our video series about biomedical innovation.
Characteristics and Properties of Polycarbonates
Polycarbonates are ideal materials and thus widely used in various medical applications and other industrial applications. They have gained popularity due it their versatile characteristics, recyclability, and eco-friendly processing. Some of the remarkable properties of polycarbonates include:
- Toughness and impact strength Polycarbonates boast of a high strength that makes them highly resistant to impact and fracture. They guarantee safety and comfort in applications that need high reliability and performance. Polycarbonates can withstand temperatures of up to 140°C and down to -20°C.
- Transparency Polycarbonates are clear plastic that can transmit over 90% of light, similar to glass. Besides, polycarbonate sheets are found in varying shades that can be customized depending on the application at hand.
- Lightweight Because of its low weight, polycarbonates provide extensive possibilities for OEMs to design depending on the end-user application. It also enhances efficiency, reduces overall transportation costs, and makes the installation process much simpler.
- UV radiation protection Polycarbonates can block UV rays and thus provide 100% radiation protection.
- Chemical resistance Polycarbonates have excellent resistance against many chemicals, including diluted acids, alcohols, aliphatic hydrocarbons, oils, and greases.
- Optical nature Because it has an amorphous structure, polycarbonate is an excellent optical property. Clear polycarbonate has a refractive index of approximately 1.584.
- Steam Sterilization Polycarbonates can also withstand repeated steam sterilizations.
Production Methods
There are about 2.7 million tons of polycarbonates produced annually across the world. The standard manufacturing process involves reacting bisphenol A and phosgene in an interfacial polymerization process. Essentially, the disodium salt of bisphenol A reacts with phosgene that is dissolved in a chlorinated organic solvent like methylene chloride to produce polycarbonates. The reaction can be carried out in one or two stages, in a batch or continuous operation.
Some of the standard methods to produce polycarbonate medical device parts include injection molding, extrusion, blow molding, and thermoforming. Typically, polycarbonates are melted and forced into a mold with high pressure to achieve the desired shape. Before processing, it is recommended that the material is dried at temperatures of 120°C. The ideal target moisture should not go past 0.02 percent.
Common Uses in Medical Devices and Life Sciences
Medical device manufacturers often use polycarbonates when creating materials due to their exceptional properties like clarity, heat resistance, toughness, and dimensional stability. It is a material of choice because manufacturers can sterilize polycarbonate using FDA-approved methods such as ETO, irradiation, and limited autoclave cycles. Some of the typical medical applications of polycarbonates include:
- Drug delivery systems
- Surgical instruments
- Blood reservoirs
- Hemodialysis membranes
- Blood filters
Renal dialysis involves the process of removing and screening blood so that toxins are removed. This process depends on passing the blood through a semi-permeable membrane cartridge, and polycarbonates can form a transparent and sturdy material to house the membrane. Polycarbonates are also resistant to chipping, shattering, and withstand several types of sterilization, and thus can be reused without compromise on performance.
In cardiac procedures, polycarbonates are used in blood oxygenators, blood filters, and reservoirs. Because they feature high transparency, polycarbonate allows doctors to monitor blood easily. Polycarbonates are also the ideal choice for intravenous connectors owing to sterilization flexibility. And because of the clarity, doctors and patients can easily track the administration of fluids. Its structural stability also enables it to fit securely with other devices.
In surgical applications, polycarbonates are replacing metal in procedures that use trocars and tube-like instruments to insert into the body. Polycarbonates prevent trocars from bending and enable doctors to track and monitor the performance of these tools efficiently.
The Best Method of Sterilization
In the medical field, sterilization is an essential factor in making devices that have direct contact with patients. One critical attribute of polycarbonates is that they can be sterilized using all the available options, including steam autoclaving, irradiation (both gamma and electron-beam), and ethylene oxide (ETO). It can also be disinfected through common clinical disinfectants like isopropyl alcohol. However, the most effective method and its suitability depend on polycarbonate material's specific properties. It is important to note that polycarbonates are not ideal for devices that require repeated autoclaving.
ARTICLES & RESOURCES
Explore materials, technologies, design, and manufacturing in the life sciences.
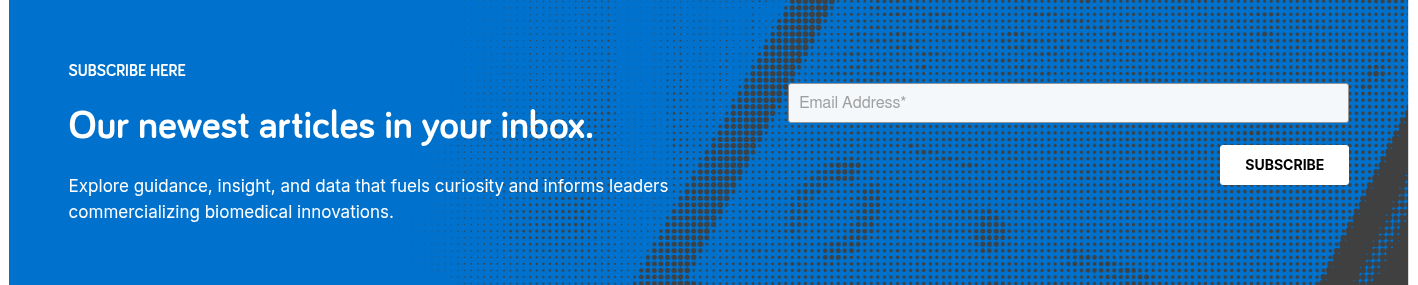